A Kecskeméti Konzerv Kft. a tavalyi évben megújította anyagmozgató gépflottáját, és ehhez olyan partnert keresett, amely a gépek mellett az összes járulékos szolgáltatást havi elszámolás keretében egy kézből biztosítja. Erről beszélgettünk a két cég vezetőivel.
A kecskeméti konzervgyár története több mint 100 éves múltra tekint vissza. Hogyan alakult a vállalat tulajdonosi köre a rendszerváltás után?
Kovács János: A Kecskeméti Konzerv Kft. elődjét, a Gyümölcs- és Főzelékkonzerv készítő Rt.-t 1900-ban alapította az osztrák Dieffenbach J. Eugen, amely Kecskemét egyik legnagyobb termelőüzeme volt több külső, nem kecskeméti telephellyel. A vállalat 1990-ig az úgynevezett 16 nagy magyar konzervgyár egyike volt, amelyek az akkori trösztöt alkották. A gyárat 1993-ban az angol Hillsdown Holdings és az amerikai H. J. Heinz alkotta konzorcium megvásárolta a magyar államtól. A konzervgyár termékportfóliója ekkor három termékkörre koncentrálódott – ez volt a legnagyobb magyar bébiételgyártó üzem, ami kifejezetten illett a Heinz profiljába, emellett jelentős sűrített paradicsom és paradicsom alapú gyártóbázissal is rendelkezett, a harmadik szegmens pedig a zöldségkonzervgyártás volt.
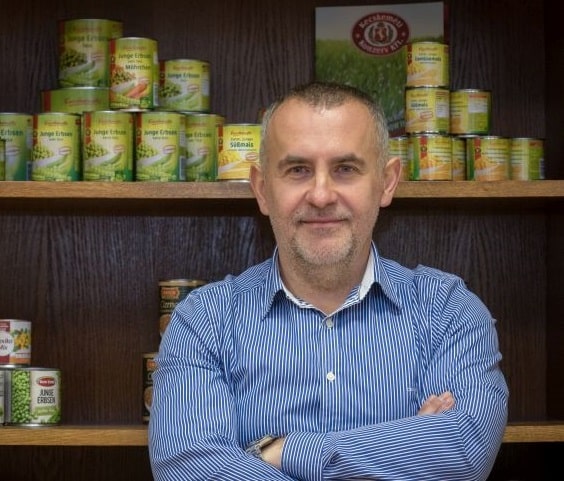
Ebben az időben még 400 különböző terméket állítottak elő az üzemben. Így szerepelt a gyártási palettán uborka, meggy, különféle lekvárok, lecsó, illetve az orosz piac által igényelt legkülönbözőbb zöldségkeverékek, mivel a termékek zöme abban az időszakban az exszovjet piacon került értékesítésre. A 90-es évek elején csupán bébiételből közel 100 különböző terméket állított elő a Kecskeméti Konzervgyár Rt., amely 1995-ben teljes egészében a Heinz tulajdonába került.
Ekkor elkezdődött a racionalizálás, ami a termékféleségek számának csökkentését eredményezte: kivették azokat a nyersanyagokat a portfólióból, amelyek termelése az időjárási és egyéb körülmények között kockázatos volt. 1998 augusztusában a nagy orosz rubelválság miatt nehéz helyzetbe került a gyár, és 1999-ben egy Kanadába kivándorolt magyar tulajdonába került, majd 2003 nyarán az Univer cégcsoport vásárolta meg.
Mivel a két vállalat termékportfóliója és értékesítési rendszere is nagyon eltért egymástól, ezért 2005 elején a tulajdonosok között olyan megállapodás született, amelynek értelmében a paradicsom- és a bébiételgyártó bázis az Univer érdekkörében maradt, a zöldségkonzervgyártó üzemet pedig Kecskeméti Konzerv Kft. néven először bérbe vettük, majd megvásároltuk az Univertől. Vagyis megalakult egy önálló jogi személy, önálló gyártóbázissal, amely azonban továbbra is kapcsolódott az Univerhez a gyártási energiaellátási rendszert tekintve. Ez, a két vállalat közötti „köldökzsinór” 2016-ig kisebb-nagyobb mértékig fennmaradt.
Az új alapokkal elindított cég mely tevékenységekre helyezte a hangsúlyt?
Kovács János: A termékportfólió kialakításánál abból a „Heinzes” logikából indultunk ki, hogy csak azt érdemes az üzemben gyártani, amit nagy szériában, megfelelő mezőgazdasági háttérrel meg lehet termeltetni Magyarországon, és ezeknek a termékeknekmegvan a felvevőpiaca. A piac jellemzően nem Magyarországot jelenti, mert a hazai zöldségkonzerv-fogyasztás volumene a mi 120 napos, klasszikus nyersanyagszezonunkból 5-6 nap alatt legyártható lenne. Kizárólag exportra, közvetlenül nagykereskedelmi hálózatok számára szállítunk Skandináviától kezdve Nagy-Britannián keresztül a Benelux államokig, illetve Olaszországig – vagyis elsődlegesen az Európai Unió a célterületünk.
A gyár már a problémás időszakban, azaz 2000-ben átállt az orosz piacról a nyugat-európai hálózatok számára való gyártásra, és ez elsősorban annak volt köszönhető, hogy a 80-as évek végén sikerült személyes kapcsolatokat kiépíteni. A gyártási volumen 2014-től dinamikusan bővült, és ma már Törökországba, illetve a közel-keleti országokba is szállítunk, mivel gyártási technológiánk és az üzemszervezésünk lehetővé teszi, hogy speciális vevői igényeknek is megfeleljenek az általunk előállított termékek.
A kóser gyártásnál egy rabbinak a folyamatos jelenlétét kell megoldanunk, amikor pedig a török partnerek jönnek, akkor nekik azt kell bebizonyítani, hogy melyik az az árutömeg a raktáron belül, amelyet csak és kizárólag az ő számukra gyártottunk. Természetesen évtizedek óta kiváló kapcsolatot tartunk fenn a hazai mezőgazdasági termelőkkel. Jelenleg két fő termékünk van, egyrészt a csemegekukorica – amely az 1970-es évek végén jelent meg Magyarországon, mint termeltethető, termelendő alapanyag –, másrészt a zöldborsó.
A két termék között alapvető különbség, hogy amíg a csemegekukorica igazi desszerttermék, addig a zöldborsó a fehérje tartalma miatt húspótlóként fogyasztható. Az első, 2006-os teljes gazdasági évben már 7 milliárd forintos árbevételt értünk el, amit 2018-ra sikerült megduplázni, azaz elérni a 14 milliárd forintot.
Mi jellemzi a gyártást?
Kovács János: Nagyjából 120 napos friss szezonunk van. Az orosz piaci igényeknek megfelelően már a 2000-es évek elején beindult a rehidratált termékek gyártása is, ami azt jelenti, hogy a száraz alapanyagot vízzel visszaduzzasztva állítunk elő konzervet. Akkor az exszovjet piacon a zöldborsónak volt nagy keletje, ma a nyugat-európai piacon a csicseriborsó, a fehér- és vörösbabok nagyon népszerűek ebben a termékkategóriában, amelyből jelentős mennyiséget lehet gyártani és értékesíteni. Hogy ez a portfólióba bekerülhetett, az a piaci igények megjelenésén túl annak köszönhető, hogy a Magyar Nemzeti Bank Növekedési Hitelprogramja keretében kedvező kamatozású beruházási hitelt kaptunk, emellett a Nemzetgazdasági Minisztérium nagyvállalati beruházási programja jelentős, közel egymilliárd forintos támogatást biztosított technológiai fejlesztésre. Ennek részeként sikerült az önálló víz-, villamos-energia, gőz- és gázellátás kialakítása, így már minden szempontból önálló szereplői vagyunk a piacnak.
A termelési volumen növekedését jól jellemzi, hogy a 2006-os, első teljes gazdasági évhez képeset, amikor is nagyjából 40 millió doboz kukoricát állítottunk elő, ma már 110 millió dobozt gyártunk évente ebből, a legnagyobb mennyiségben termelt termékünkből. Ahhoz persze, hogy a gyártási volument növelni tudjuk – miután a termelés tekintetében az időjárás és a szezon adottságaihoz kell igazodnunk –, a napi kapacitásokat kell emelnünk. Mostanra eljutottunk oda, hogy a kezdeti, nagyjából napi 550-600 ezer doboz legyártott konzervet 1,6 millió dobozra emeltük. Ez első pillantásra egyszerűnek tűnik, hiszen mindössze két fő terméket gyártunk.
Egészen más a kép azonban, ha figyelembe vesszük, hogy a nyugat-európai piacon a borsót csak méret szerint osztályozva lehet eladni, s ott annál értékesebb a borsó, minél kisebb a mérete. Pedig tény, hogy minél nagyobb a borsó, annál nagyobb a belső, puha része, s minél kisebb, arányaiban annál több a keményebb külső héj. De ha ezt igényli a piac, akkor mi természetesen ezt szállítjuk. Hogy ennek az igénynek is meg tudjunk felelni, speciális vetőmagokkal termeltetjük a borsót. De a méret csak egy tényező, az ízesítés a másik, hiszen van, aki sok cukorral szereti, van, aki natúr, de olyan is akad, aki a sósat kedveli.
Egy harmadik osztályozó tényező a doboz nagysága, ami csupán a borsó esetén közel 40 különböző kiszerelést jelent. És akkor még az is kérdés, hogy legyen vagy ne legyen a csomagoláson tépőzár, keverjünk bele bébirépát vagy ne. A csemegekukorica termékeknél hasonló szempontrendszert kell figyelembe venni. Emellett például a klasszikus, normál csemegekukorica esetében az édes ízt répacukor hozzáadásával lehet elérni, de ez a fajta termék, ami 10 évvel ezelőtt még a gyártás 90%-át adta, ma 5% alatt van.
Jelenleg az úgynevezett super sweet fajták iránt van igény, ami nem igényli répacukor hozzáadását, mivel maga a növény biztosítja az édes ízt. Ebből is többféle kiszerelést szállítunk, mind az egyedi fogyasztók igényeinek kielégítésére, mind a HoReCa ügyfelek részére, mely utóbbi szegmensben is jelen vagyunk piacvezető szinten évi 5 millió dobozzal. És ugyanez mondható el a rehidratált termékekről is. Arra büszkék vagyunk, hogy megengedhetjük magunknak azt a luxust, hogy kizárólag szerződésre gyártunk. A minőségre kiemelt hangsúlyt helyezünk, hiszen termékeink 100%-ban az európai piacokon kerülnek értékesítésre, így természetesen rendelkezünk IFS és BRC minőségirányítási rendszerekkel.
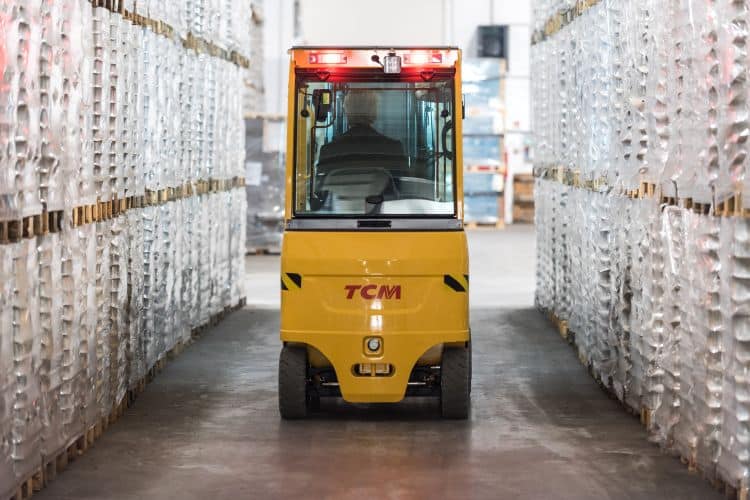
Az infrastruktúra oldaláról hogyan tudták kiszolgálni ezt a dinamikus termelésbővülést?
Kovács János: A termelés ilyen mértékű felfutása értelemszerűen a volumen kiszolgálásához szükséges infrastruktúra bővülésével is járt, akár a raktárkapacitásokat, akár az anyagmozgató gépparkot és a létszámot tekintjük. Az elmúlt két évben a saját telephelyünkön egy 12 000 négyzetméteres raktár építésével viszonylag jelentős lépést tettünk az infrastruktúra fejlesztésében, hiszen korábban nemcsak a saját telephelyünkön, hanem Kecskeméten, bérelt raktárakban is tároltuk az árukat.
Az újonnan épített raktár azonban nem elegendő, mert még így sem vagyunk önellátók a tárolási kapacitás szempontjából. Ezért egy újabb raktár építésében gondolkodunk az elkövetkezendő években, és az ehhez szükséges területeket már megvásároltuk. Már csak kedvező finanszírozási feltételekre várunk, hogy az igényeinket tökéletesen kielégítő raktár építésébe kezdjünk. Ha ez sikerül, akkor jön el az a logisztikai és üzemszervezési szempontból ideális állapot, amikor is egy telephelyen belül tudunk majd mindent mozgatni.
Alapanyagoldalról ez milyen nagyságrendet képvisel?
Kovács János: A frissárut tekintve, éves szinten 90 000 tonna nyersanyagot kell a gyárba beszállítani. A borsót szem formájában hozzuk be, mert a betakarítástól számított 4-6 órán belül fel kell dolgozni, különben minőségromlással lehet számolni, ezt pedig nyilvánvalóan nem engedhetjük meg magunknak. A kukoricakonzervhez csöves betakarított kukoricát szállítunk be, amit aztán lefosztunk, levágjuk a szemeket és azt tesszük a dobozba. Ez egyben azt is jelenti, hogy a bejövő alapanyag 60%-a el is hagyja a gyár területét, leginkább állattartó telepekre kerül vagy biogáz alapanyagot előkészítő vállalkozásokhoz.
Vagyis tekintélyes mennyiségű anyagról van szó, és ennek kezelése ebben a fuvarozási kapacitás hiányos világban nem egyszerű dolog. Nem is beszélve a munkaerőhiányról, ami Kecskeméten is igen nehéz helyzetet teremt. Nekünk az a szerencsénk, hogy nagyon kevés magasan képzett munkaerő szükséges a gyártáshoz, viszont a folyamataink kevésbé automatizálhatók. Egy autógyárban adott a sztenderdizálás és a robotizálás lehetősége, ami a mi gyártásunkra nem jellemző. Például van olyan berendezésünk, amelyen a sztenderdtől eltérő színű és alakú kukoricát vagy borsót kiszedjük a gyártóvonalon továbbított alapanyagok közül, de az, hogy mi a nem sztenderd termék, azt magától egy berendezés nem tudja eldönteni.
Ehhez adódik még az is, hogy minden évben más jellegű probléma merül fel, mert a borsószem egy adott évben nem ugyanolyan, mint a rákövetkező évben. Egyszóval ezt a munkafolyamatot nem lehet automatizálni. Ez úgynevezett „hangyaszövetkezet” volt és az is maradt. Nálunk az emberek hoznak döntést a feldolgozási folyamat során.
Mi jellemzi a konzervgyári anyagmozgatást?
Kovács János: Jelenleg mintegy 90 000 raklapnyi címkézetlen félkészárut állítunk elő éves szinten a gyártási szezonban, és ezt részben a saját raktárunkban, részben pedig külső raktárban készletezzük. Ezt a volument kétszer – egyrészt a vevői megrendelések alapján történő címkézéshez, másrészt a csomagolás utáni átmeneti tároláshoz – meg kell mozgatnunk. Ehhez jön még a kamionokra rakodás ugyanerre a volumenre vetítve, tehát nálunk az anyagmozgatási igény igen nagy. Ideális esetben is minden egyes terméket legalább háromszor kell megmozgatni. Ehhez egy megbízható targoncaflottára van szükségünk.
A tavalyi évben vizsgáltuk felül az anyagmozgató gépparkunkat, amellyel évek óta kiszolgáljuk a termelést és a raktározási igényeinket, viszont ennek a flottának a futott üzemóra ideje 35 000 óra. Tehát azt is mondhatnám, hogy eljárt felettük az idő, de egyben azt is jelenti, hogy nagyon megbecsüljük az eszközeinket, hiszen egy targoncát 15-20 ezer óra futásidő után rendszerint üzemen kívül helyeznek.
A tavalyi évben a folyamatos volumennövekedés okán szükségessé vált az anyagmozgató gépflotta frissítése. A korábbi években ugyan próbálkoztunk az igényeinket szezonban bérelt gépekkel lefedni, illetve amikor állami támogatást is igénybe vehettünk, akkor vásároltunk néhány gépet. A tavalyi évben viszont a teljes régi gépflotta cseréje mellett döntöttünk. Cél volt, hogy az anyagmozgató gépekhez kapcsolódó összes tevékenységet – karbantartást, műszaki felügyeletet stb. – kiszervezzük, tehát egy kézből szerezzük be az összes szolgáltatást, és a hó végén csupán egy számlát kelljen kezelnünk.
Emellett maradt néhány saját targoncánk, amelyekhez kapcsolódóan az apróbb javításokat is a tenderen kiválasztott céggel kívántuk elvégeztetni. Pályázatot írtunk ki, és az előzetes igényfelmérés alapján kialakítottuk azt a feltételrendszert, amely a döntés alapjául szolgált a megfelelő géppark kialakítására. Két céget kértünk fel az ajánlattételre, végül a választásunk a Nagoya Kft.-re esett.
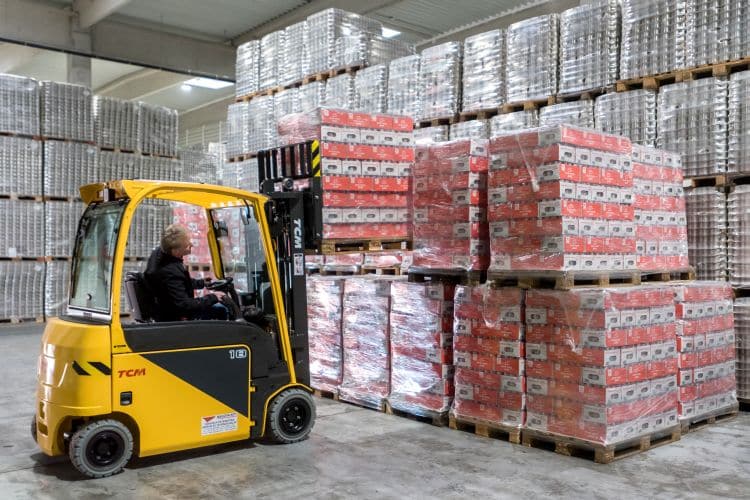
Miért éppen a japán TCM targoncákat forgalmazó Nagoya Kft.-t választották?
Kovács János: A Nagoya Kft.-vel már a 90-es évek eleje óta együtt dolgozunk, főként a gyárban korábban üzemelő saját gépeink karbantartása és szervizelése területén. Kiemelném, hogy a most lecserélt gépeinket, mint már említettem, 35 000 üzemórával selejteztük ki, és ez a magas óraszám annak köszönhető, hogy a gépek a teljes élettartam alatt megfelelő és szakszerű karbantartásban részesültek. Emellett a választásnál természetesen a bekerülési ár fontos szempont volt, azonban nem minden fejezhető ki számértékben. Lényeges az évek során tapasztalt gyors, precíz és megbízható szervizszolgáltatás, amit a Nagoya Kft. több 10 éve biztosított a számunkra.
Hány gépet szereztek be és ezekkel milyen munkafolyamatokat szolgálnak ki?
Kovács János: Öt évre szóló bérleti szerződés keretében 15 gépet szereztünk be, amelyekkel a 12 000 négyzetméteres, 4 szekcióra osztott raktárcsarnokban naponta mintegy 2000 tonnát mozgatunk meg.
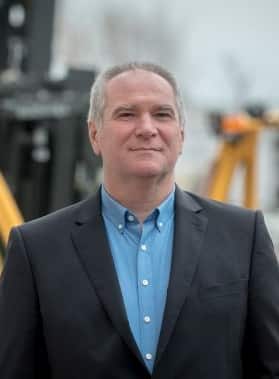
Horváth Béla: A 13 gázüzemű és 2 elektromos TCM targonca, amely az idei év elején állt üzembe a konzervgyárban, kifejezetten kezelőbarát, jól felszerelt gépek, teljes közúti (LED) világítással és prémium üléssel. A raktárban a késztermékek és a göngyölegek mozgatásához 1 darab TCM FGE25-E1 gázüzemű homlokvillás targoncát szállítottunk, amely triplex 7000 mm-es emelési magasságú oszloppal, integrált oldalmozgatóval, villavízszintezővel, fűthető acélkabinnal felszerelt.
A késztermék-kiszállítás kiszolgálására, illetve a raktár és a gyártóvonalak közötti anyagmozgatásra 6 darab, szintén TCM FGE25-E1 típusú, gázüzemű homlokvillás targoncát szállítottunk, amelyek mindegyike triplex 5500 mm-es emelési magasságú oszloppal ellátott.
A teherautók le- és felrakodását 3 darab TCM FGE 25-E1 gázüzemű homlokvillás targoncával végzik a kecskeméti konzervgyár raktárában. Ezek közül 2 darab 3300 mm-es, 1 pedig triplex 4750 mm-es emelési magasságú oszloppal ellátott. Ezeknek a gépeknek a különlegessége, hogy mindegyik integrált oldalmozgatóval, KAUP 2T 140 SV villakitolóval felszerelt, amelynek segítségével egyoldalról történik a teherautók le- és felrakodása, nincs szükség a teherautó megkerülésére, illetve mindkét oldali ponyvázására.
Mind beltéri, mind kültéri anyagmozgatásra 2 darab FGE18-E1 gázüzemű homlokvillás targoncát használnak a kecskeméti üzem területén, amelyek triplex 4750 mm-es emelési magasságú oszloppal, integrált oldalmozgatóval, villavízszintezővel, esővédőtetővel, első és hátsó szélvédővel, valamint 1100 mm-es emelővillával ellátott. A göngyölegek és a hulladék kezelését 1 darab FGE18-E1 gázüzemű, triplex 4750 mm-es emelési magasságú oszloppal, villavízszintezővel, fűthető acélkabinnal szerelt homlokvillás gép végzi, amely KAUP1,5 T 451W/180 típusú, szorítópofás forgatóművel felszerelt, valamint gyorscsatlakozóval ellátott.
A csomagolóüzemben 2 darab TCM FB18-E1 típusú elektromos, triplex 4750 mm-es emelési magasságú oszloppal, integrált oldalmozgatóval ellátott 4 támaszú homlokvillás targonca teljesít szolgálatot.
Hogyan értékelik az együttműködést?
Kovács János: Hosszú időre szerződtünk, így kiemelten fontos a bizalomra épített partnerkapcsolat. Ha probléma van, azt nyíltan el kell mondani, és közösen megtalálni a megoldást. Ez csak jó kommunikációval érhető el.
Horváth Béla: A Kecskeméti Konzerv Kft. egy korrekt, megbízható partner. A cég vezetése számára az az elsődleges, hogy olyan üzembiztos flottával rendelkezzenek, amely az anyagmozgatás-intenzív szezonban – tehát abban a 120 napban, amikor a friss kukorica és borsó feldolgozása történik – is megbízhatóan, hiba nélkül teljesít, hiszen ebben a periódusban már csak egy gép kiesése is komoly fennakadást jelentene a termelésben.
A kiválasztás során az volt a céljuk, hogy reális piaci áron egy olyan flotta kerüljön beszerzésre bérleti konstrukció keretében, amely hosszú távon jól teljesít, és az ehhez kapcsolódó összes szolgáltatás egy kézből elérhető legyen. Ez azt jelenti, hogy egy hónapban egy számlát állítunk ki az összes felmerülő költségről, és nincsenek rejtett tételek. A full szerviz nálunk valóban a teljes körű szervizszolgáltatást jelenti.
Forrás: https://www.scmonitor.hu